Introduction
Peanut (Arachis hypogaea L.) is one of the most economically important oilseed and feed crops globally. In the southern US, yield and quality of peanuts are reduced by the invasion of Aspergillus flavus and A. parasiticus during production, harvest, storage, and processing. The optimal growth conditions for these pathogens are ambient temperatures between 82 and 98 °F, soil pH of 3.5–8, and high relative humidity (>85%).1 These fungal pathogens are soil-borne (soil dwellers) and infect peanut seeds and plants after direct contact with them. The pathogens can both reduce yield and contaminate the crop with aflatoxins. Widespread aflatoxin contamination often occurs in hot and humid agro-ecological zones.2
Aflatoxins are poisonous chemicals produced by A. flavus and A. parasiticus. These lethal toxins pose a threat to the food and feed industry. Aflatoxins are the most potent carcinogens (cancer-causing substances) and are known to cause liver cancer in humans and animals.3 Aspergillus species infect a broad range of crops such as peanut, corn, pistachio, cotton, tree nuts, chili, and black pepper4 and contaminate the produce with aflatoxins.5 Aflatoxins are classified into different groups depending on the fluorescence they emit upon exposure to ultraviolet (UV) light. Aflatoxins that emit blue fluorescence in UV light are labeled B1 and B2, green fluorescence – G1, and green-blue fluorescence – G2. Each Aspergillus species does not produce all aflatoxins. For example, A. parasiticus produces aflatoxins B1, B2, G1, and G2, while A. flavus only produces B1 and B2.6-10 Among the aflatoxin groups, aflatoxin B1 is the most potent carcinogen. Crops need to be monitored continuously for the presence of aflatoxin producing Aspergillus species through all stages of production.
Pathogen Biology and Identification
Knowledge about the biology of the pathogen is helpful in its sustainable management. Information about the most vulnerable stage of pathogen development helps time management so that it occurs during that stage. Aspergillus flavus and A. parasiticus live in soil and transmit the spores through the air. These pathogens overwinter in the soil and plant debris for as long as three years, depending on ambient conditions. When contact with the new crop occurs, the pathogen can infect it and produce spores that further transport the pathogen by the wind. Because it is soil-borne, the pathogen infects the below-ground plant parts when in contact with the peanut plant. The initial symptoms in infected pods give them a whitish-green moldy appearance. Moreover, the fungal patches on pods are light gray-green to dark-green in color with whitish margins. Figure 1 illustrates the symptoms of A. flavus and A. parasiticus infection of peanut in the field.
The life cycle of A. flavus and A. parasiticus is divided into two phases: (1) overwintering and colonization of plant debris in soil, and (2) infection and infestation of crop tissue such as root, pegs, and seeds (peanut pods). Soil is the primary source of infection for both pathogens. At the beginning of the growing season (spring) and occasionally at the end of winter, the sclerotia (i.e., the compact resting mass of mycelium with darkened rind) are exposed to the soil surface under favorable environmental conditions (i.e., hot [>77°F] and dry weather). The sclerotia promptly germinate and produce new conidia (asexual spore) that serve as a new source of inocula that spreads via insects or wind to new plants. Infected plants also serve as a secondary source of infection.11,12 The pathogen continuously colonizes and infects the new crop and produces aflatoxin, as elaborated in figure 2. Infection severity increases when drought, high temperatures, and high humidity simultaneously occur.12
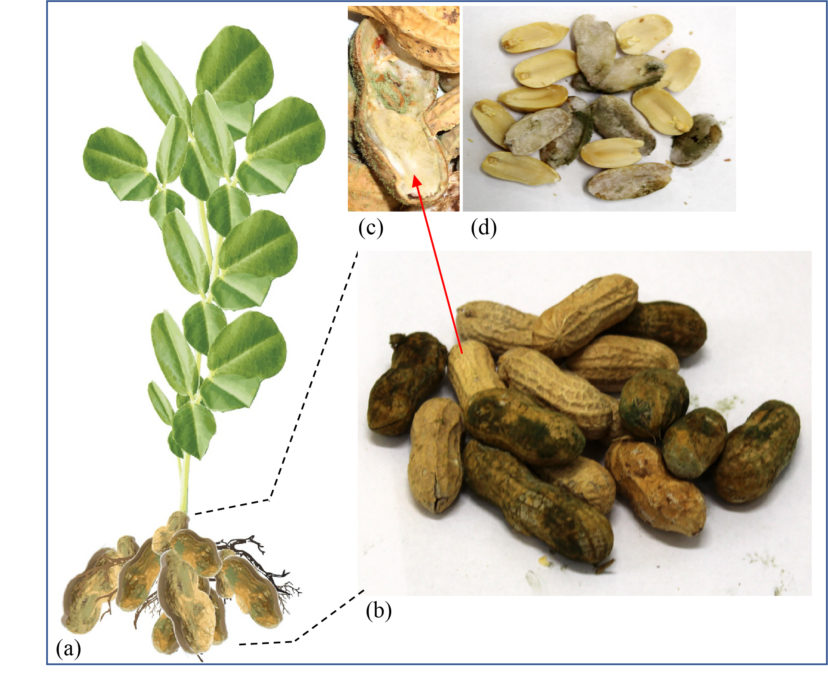
Figure 1. Pods infected by Aspergillus flavus and A. parasiticus (a). Closeup of pods shells (b) and peanut kernels (c) showing symptoms of infection. Section (d) shows sporulation (spore production) on the surface of peanut seeds. Image credit: Tariq Alam, Clemson University.
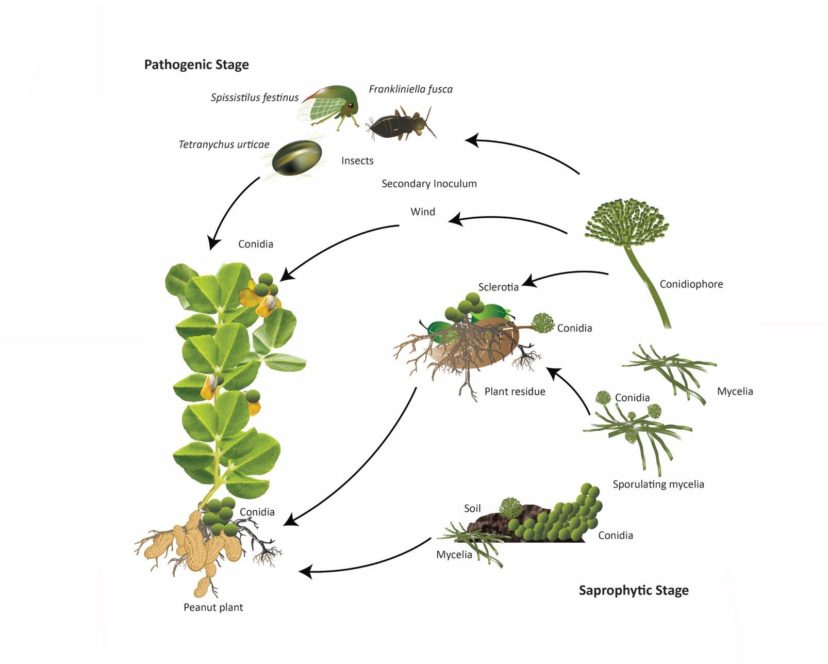
Figure 2. The life cycle of Aspergillus flavus and A. parasiticus in peanut. Notice the wind/insect-mediated delivery of conidia to above-ground plant parts, such as flowers and developing pegs, which occasionally lead to the fungal infestation upon anchoring of the pegs in the soil.13 Image credit: Tariq Alam, Clemson University.
Food and Drug Administration (FDA) Regulatory Standards for the Food Aflatoxin Content
Total aflatoxin levels in foods are limited to avoid unintentional exposure of consumers and livestock to aflatoxins. Guidelines from the FDA permit, at most, 20 µg.kg1 (ppb – parts per billion) of total aflatoxins in food or feed and 0.5 ppb cumulative aflatoxins in milk. The European Union aflatoxin limit is stricter, allowing a maximum of 4 ppb for total aflatoxins and 2 ppb for aflatoxin B1. The FDA and the United States Department of Agriculture (USDA) monitor the aflatoxin content in peanuts and derived products.
Aflatoxin Contaminated Products
Aflatoxins can be found in peanuts, peanut-derived products, and animal by-products (figure 3). Animal by-products, including milk, meat, and egg, can also be contaminated with aflatoxins when animals consume feed contaminated by Aspergillus species.14,15 Aflatoxins in milk, known as Aflatoxin M1, pose a threat to the life of infants. Aflatoxin contamination of the mother’s milk occurs when the mother consumes aflatoxin-contaminated products.16
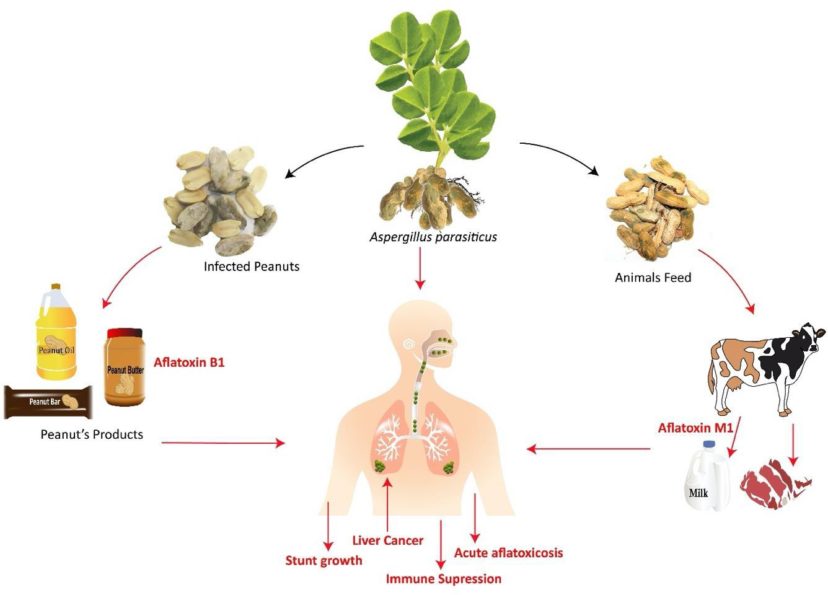
Figure 3. Sources of aflatoxin exposure and its flow in the food chain. Image credit: Tariq Alam, Clemson University.
Aflatoxin Detection in Peanut
Aflatoxins can be detected in peanuts and derived products using a variety of diagnostic tests. For this purpose, growers can use the diagnostic services offered by various public laboratories. Samples can be mailed to a nearby diagnostic facility (see the USDA approved list of laboratories17).
Sampling Procedure for Peanut Aflatoxin Contamination Test
Samples should be prepared by or in the presence of a USDA recognized inspector to obtain the aflatoxin screening certificate. Generally, aflatoxin contamination in peanut does not occur uniformly in a batch of kernels. Therefore, an ideal method is to make a composite sample consisting of subsamples taken from each part of the bin, from different loads or peanut lots, or a combination of both. The accuracy of the aflatoxin test result depends on the use of the correct sampling procedure. Use one of the following sampling strategies to collect a sample:
- For in-shell peanut with lot weight 220 lbs or less, collect ten samples with a total weight of 4.40 lbs.
- For shelled peanut kernels with a lot-weight of 220 lbs or less, collect ten samples with a total weight of 2.20 lbs.
- For in-shell peanut with lot weight between 2,201 and 4,400 lbs, collect forty samples with a total weight of 17.63 lbs.
- For shelled peanut kernels with a lot-weight between 2,201 and 4,400 lbs, collect forty samples with a total weight of 8.81 lbs.
- Mail the sample to a USDA approved laboratory for aflatoxin detection.
The recommended sample size mentioned above for the lot weight between 2,201 and 4,400 lbs is based on the USDA recommendations for the pistachio aflatoxin certification.18 The moisture content of in-shell or shelled peanuts must be less than 9%. Aflatoxin test results from the peanut samples with high-moisture content were not consistently accurate.
Pre-Harvest Aflatoxin Mitigation Strategies
Use of Resistant Varieties
The most effective strategy for the control of aflatoxin contamination is the use of resistant varieties. At present, no peanut variety is completely resistant or immune to Aspergillus species. However, moderately resistant varieties, such as FloRun™‘107’ (Florunner)19 and Tifguard,20 are available for production. While Tifrunner and Florida-07 show reduced Aspergillus infection, they are susceptible to aflatoxin accumulation.21
Timely Irrigation
In the southern US, temperature and humidity generally remain high during the peanut growing season. High-temperature and drought create conditions conducive for Aspergillus flavus and A. parasiticus infection and aflatoxin production. 22 Therefore, it is recommended to timely irrigate the crop for pathogen management. Irrigation not only relieves drought stress but also decreases soil temperature.
Commercial Bio-Control Products and RNA Interference Spray
The application of eco-friendly commercial bio-control agents can effectively control Aspergillus flavus and A. parasiticus invasion and aflatoxin production. Afla-Guard® is a bio-control that inhibits the growth of aflatoxin producing pathogen in peanut when preventatively applied. ‘Aflasafe SN01’ is another bio-control product developed and used in many countries across Africa to manage aflatoxin in peanut. This product is not yet available for use in the US. Researchers at the Clemson Department of Plant and Environmental Sciences are working to develop an environment-friendly RNA interference (RNAi)-based spray for sustainable management of Aspergillus species. This RNAi based spray is currently being evaluated in the laboratory and will be available to manage aflatoxin contamination of peanuts after the necessary testing and approval process.
Calcium
Application of calcium can reduce the level of aflatoxin contamination in peanut.23
Insect Management
During the crop growing season, different insects such as confused flour beetle (Tribolium confusum), thrips (Frankliniella fusca), three-cornered alfalfa hopper (Spissistilus festinus), and two-spotted spider mite (Tetranychus urticae) transfer Aspergillus flavus and A. parasiticus propagules (spores) from infected pegs and flowers to healthy plants. Also, insect infected peanut kernels are more likely to experience pre-harvest Aspergillus infection and exhibit aflatoxin contamination.24,25 Therefore, surveillance and timely management of peanut infesting insects is a critical control strategy. Insects can also infect harvested products during storage. During storage, control insect pests by applying the appropriate chemical pesticide. For insect pesticide selection, refer to the Peanut Insect Management guide developed by Anco.26
Early Harvesting
On-time harvest can limit the level of aflatoxin contamination.27 Rain late in the growing season generally leads to an increase in fungal growth and aflatoxin contamination. Early harvest dates differ from state to state and range from September through October (Alabama [Sep. 4], Florida [Aug. 15], Georgia [Sep. 5], New Mexico [Oct. 1], North Carolina [Sep. 24], Oklahoma [Sep. 2], South Carolina [Sep. 8], Texas [Sep. 7], and Virginia [Sep. 15].) Early harvest is not possible in certain agro-ecological zones and may not be the most economically profitable decision, depending upon production conditions. Growers should consider the impact of all harvesting decisions on resulting crop economic value and consult their county extension agent before implementing an early harvest plan.
Crop Rotation
Peanut rotation with a non-host crop is an effective strategy for breaking the infection cycle to reduce Aspergillus inoculum in the field. Of the factors considered when selecting a suitable crop for rotation, most importantly, the crop should not be a host to insect or fungal pests that infect both crops. Many vegetables are unsuitable rotation crops for peanut due to overlapping susceptibility to nematodes or fungal pests. Sweet potato is a suitable rotation crop for use with peanut.
Cultural Practices
The application of farmyard manure and lime reduces pathogen infection and aflatoxin accumulation in peanut.28
Weed Management
Common weeds such as palmer amaranth (Amaranthus palmeri), common cocklebur (Xanthium strumarium), sicklepod (Senna obtusifolia), common lambsquarters (Chenopodium album), smartweed, (Polygonum pensylvanicum) common ragweed (Ambrosia artemisiifolia), pitted morning glory (Ipomoea lacunosa), entireleaf morning glory (Ipomoea hederacea), velvetleaf (Abutilon theophrasti), broadleaf signalgrass (Urochloa platyphylla), eclipta (Eclipta prostrata), jimsonweed (Datura stramonium), and redroot pigweed (Amaranthus retroflexus) as well as volunteers like cowpea and corn, act as alternate hosts to Aspergillus species. Therefore, the proper management of weeds is a vital disease control strategy. Growers can use WebHADSS29 (Herbicide Application Decision Support System), developed by the North Carolina State Extension program, for assistance in making an economic decision about the use of herbicides. For more information on herbicide use, refer to the Peanut Weed Management guide.30
Post-Harvest Aflatoxin Mitigation Strategies
The post-harvest and preprocessing period is vital for peanuts in terms of minimizing pathogen growth and aflatoxin production. The following storage management strategies focus on reducing fungal inoculum by creating an environment that is non-conducive for infection.
Storage Conditions
Generally, aflatoxins are more concentrated in peanut seeds. Aflatoxin producing pathogens infect stored seeds and produce toxins when pod moisture level is above 8% and ambient temperature exceeds 25°C (77F).31 Dry pods to 7% moisture content to control the growth of aflatoxin producing pathogens. After drying, pods can be safely stored at 70% relative humidity and between 25–27C (77–81F) temperature for nearly one year.32 Insects and pests can infect peanuts during storage and should be controlled via the application of chemical pesticides.
Equipment Sanitization
Pathogens can survive in the soil or mud attached to harvesting equipment. Remove caked-on soil from harvest equipment before exiting the field to limit the spread of pathogens from field to field. Harvesting and drying equipment, including storage bins, should be sanitized before each use.
Packaging
Packaging material and process significantly influence aflatoxin production in peanuts. Quality deterioration and aflatoxin production in peanuts can be controlled by using hermetic zero oxygen packing.33
Separation of Infected and Healthy Pods
Peanut pods or kernels damaged by insect pests or mechanical injury during digging or threshing are more susceptible to fungal infection during storage. Identify and destroy the damaged, shriveled, misshaped, or contaminated pods and seeds.
Worker Protection from Exposure to Spore Dust
It is essential to wear appropriate personal protection equipment (PPE) when dealing with peanut pods infected with Aspergillus species. Always wear a respirator that can filter fine particles such as N95, N99, or N100. Even a single infected pod can liberate millions of spores, which, if inhaled, can cause severe reactions. Frequently change or decontaminate the PPE and harvesting equipment during the harvest.
Acknowledgments
This work was supported by the National Peanut Board, SC Peanut Board, and NIFA Hatch/Multistate grant (S009).
References Cited
- Wheeler KA, Hurdman BF, Pitt JI. Influence of pH on the growth of some toxigenic species of Aspergillus, Penicillium and Fusarium. International Journal of Food Microbiology. 1991 Feb;12(2-3):141–149. doi:10.1016/0168-1605(91)90063-U.
- Marin S, Ramos AJ, Cano-Sancho G, Sanchis V. Mycotoxins: occurrence, toxicology, and exposure assessment. Food and Chemical Toxicology. 2013 Oct;60:21–237. doi:10.1016/j.fct.2013.07.047.
- Wogan GN, Hecht SS, Felton JS, Conney AH, Loeb LA. Environmental and chemical carcinogenesis. Seminars in Cancer Biology. 2004 Oct;14:473–486. doi:10.1016/j.semcancer.2004.06.010.
- Alshannaq A, Yu JH. Occurrence, toxicity, and analysis of major mycotoxins in food. International Journal of Environmental Research and Public Health. 2017 Jun;14(6):632. doi:10.3390/ijerph14060632.
- Abbas HK, Zablotowicz RM, Bruns HA, Abel CA. Biocontrol of aflatoxin in corn by inoculation with non- aflatoxigenic Aspergillus flavus isolates. Biocontrol Science and Technology. 2006;16(5):437–449. doi:10.1080/09583150500532477.
- Abbas HK, Zablotowicz RM, Weaver MA, Horn BW, Xie W, Shier WT. Comparison of cultural and analytical methods for determination of aflatoxin production by Mississippi Delta Aspergillus isolates. Canadian Journal of Microbiology. 2004;50(3):193–199. doi:10.1139/w04-006.
- Fortnum BA. Effect of environment on aflatoxin development in preharvest maize. In: US Universities. CIMMYT Maize Aflatoxin Workshop; 1987 Apr 7–11; El Batan, Mexico. Mexico: CIMMYT; 1987.
- Heathcote JG, Hibbert JR. Aflatoxins: chemical and biological aspects. Amsterdam (The Netherlands): Elsevier Scientific Publishing Co.; 1978.
- Hill RA, Wilson DM, McMillian WW, Widstrom NW, Cole RJ, Sanders TH, Blankenship PD. Ecology of the Aspergillus flavus group and aflatoxin formation in maize and groundnut. In: Lacey J, ed. Trichothecenes and other mycotoxins. Chichester (UK): John Wiley and Sons; 1985. 79–95.
- Jones RK, RK J, HE D. Effect of nitrogen fertilizer, planting date, and harvest date on aflatoxin production in corn inoculated with Aspergillus flavus. Plant Disease. 1980; 65(9):741–744. https://www.apsnet.org/publications/PlantDisease/BackIssues/Documents/1981Articles/PlantDisease65n09_741.PDF
- Horn BW. Biodiversity of Aspergillus section Flavi in the United States: a review. Food Additives and Contaminants. 2007; 24(10):1088–1101. doi:10.1080/02652030701510012.
- Payne GA, Widstrom NW. Aflatoxin in maize. Critical Reviews in Plant Sciences. 1992; 10(5):423–440. doi:10.1080/07352689209382320.
- Amaike S, Keller NP. Aspergillus flavus. Annual Review of Phytopathology. 2011 Sep 8;49:107–33. doi:10.1146/annurev-phyto-072910-095221.
- Armorini S, Altafini A, Zaghini A, Roncada P. Occurrence of aflatoxin M1 in conventional and organic milk offered for sale in Italy. Mycotoxin Research. 2016;32(4):237–246. doi:10.1007/s12550-016-0256-8.
- Iqbal SZ, Nisar S, Asi MR, Jinap S. Natural incidence of aflatoxins, ochratoxin A and zearalenone in chicken meat and eggs. Food Control. 2014;43:98–103. doi:10.1016/j.foodcont.2014.02.046.
- Cantú-Cornelio F, Aguilar-Toalá JE, de León-Rodríguez CI, Esparza-Romero J, Vallejo-Cordoba B, González- Córdova AF, García HS, Hernández-Mendoza A. Occurrence and factors associated with the presence of aflatoxin M1 in breast milk samples of nursing mothers in central Mexico. Food Control. 2016;62:16–22. doi:10.1016/j.foodcont.2015.10.004.
- Official listing of USDA and USDA-approved laboratories, laboratory approval program for analysis of aflatoxins. Washington (DC): United Stated Department of Agriculture; 2020 [accessed April 29, 2020]. https://www.ams.usda.gov/sites/default/files/media/OfficialListingofLAPAflatoxinUSDAApprovedLaboratories.pdf
- Pistachios grown in California, Arizona, and New Mexico. 7 CFR 983. [accessed June 22, 2020]. https://www.govinfo.gov/content/pkg/CFR-2011-title7-vol8/pdf/CFR-2011-title7-vol8-part983.pdf.
- Kolte SJ. Diseases of annual edible oilseed crops: volume I: peanut diseases. Boca Raton (FL): CRC Press; 2019. P 158.
- Timper P, Wilson DM, Holbrook CC. Contribution of root-knot nematodes to aflatoxin contamination in peanut (Arachis hypogaea). Peanut Science. 2013;40(1):3–-39. doi:10.3146/PS12-14.1.
- Korani WA, Chu Y, Holbrook C, Clevenger J, Ozias-Akins P. Genotypic regulation of aflatoxin accumulation but not Aspergillus fungal growth upon post-harvest infection of peanut (Arachis hypogaea L.) seeds. Toxins. 2017;9(7):218. doi:10.3390/toxins9070218.
- Payne GA, Brown MP. Genetics and physiology of aflatoxin biosynthesis. Annual Review of Phytopathology. 1998;36(1):329–362. doi:10.1146/annurev.phyto.36.1.329.
- Uppala SS. Factors affecting pre-harvest aflatoxin contamination of peanut (Arachis hypogaea L.). Aurburn (AL): Auburn University; 2011. http://hdl.handle.net/10415/2703.
- Hill RA, Blankenship PD, Cole RJ, Sanders TH. Effects of soil moisture and temperature on preharvest invasion of peanuts by the Aspergillus flavus group and subsequent aflatoxin development. Applied and Environmental Microbiology. 1983;45(2):628–633. https://aem.asm.org/content/aem/45/2/628.full.pdf.
- Pitt JI, Wild CP, Baan RA, Gelderblom WCA, Miller JD, Riley RT, Wu F (editors). Improving public health through mycotoxin control. Lyon, (France): International Agency for Research on Cancer; 2012; IARC Scientific Publications Series, No. 158.
- Anco D. Peanut insect management. South Carolina pest management handbook for field crops 2017. Clemson (SC): Clemson University; 2017 [accessed April 29, 2020]. https://www.clemson.edu/extension/agronomy/pestmanagement17/insect%20control%20peanuts.pdf.
- Rachaputi N, Krosch S, Wright GC. Management practices to minimise pre-harvest aflatoxin contamination in Australian peanuts. Australian Journal of Experimental Agriculture. 2002;42(5):595–605. doi:10.1071/EA01139.
- Waliyar F, Kumar PL, Traoré A, Ntare BR, Diarra B, Kodio O. Pre-and post-harvest management of aflatoxin contamination in peanuts. Mycotoxins: Detection Methods, Management, Public Health and Agricultural Trade. Wallingford (UK): CAB International; 2008:209–218.
- Jordan DL, Lassiter BR. The herbicide application decision support system for field crops. Raleigh (NC): North Carolina State University; 2009 [accessed April 29, 2020]. http://www.webhadss.ncsu.edu.
- Jordan, DL. Peanut weed management. Raleigh (NC): North Carolina State University, North Carolina State Extension; 2020 [accessed April 29, 2020]. https://content.ces.ncsu.edu/peanut-information/peanut-weed-management.
- Tola M, Kebede B. Occurrence, importance and control of mycotoxins: a review. Cogent Food & Agriculture. 2016;2(1):1191103. doi:10.1080/23311932.2016.1191103.
- Torres AM, Barros GG, Palacios SA, Chulze SN, Battilani P. Review on pre-and post-harvest management of peanuts to minimize aflatoxin contamination. Food Research International. 2014;62:11–19. doi:10.1016/j.foodres.2014.02.023.
- Darko C, Mallikarjunan PK, Kaya-Celiker H, Frimpong EA, Dizisi K. Effects of packaging and pre-storage treatments on aflatoxin production in peanut storage under controlled conditions. Journal of Food Science and Technology. 2018;55(4):1366–1375. doi10.1007/s13197-018-3051-z.